Label-Competence-Center: Our in-house laboratory
Standardized labels? We can do that. But we offer much more than that. Because for inotec, it goes without saying that we also want to offer customers outstanding service and innovative solutions. Internal quality assurance and product development are very important for this. That's why we have set up our own department for this purpose, where experts use standardized test procedures to put our labels to the test and develop them further. We call it our Label Competence Center (LCC).
Quality assurance and development of labels
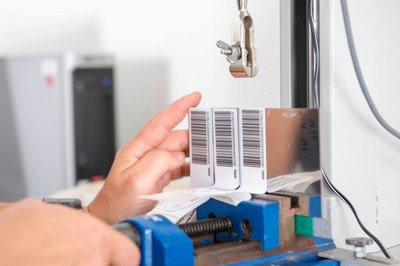
On the one hand, our Label Competence Center (LCC) is a classic quality assurance department. It was initially established as a laboratory for internal product tests. For the past 20 years, however, it has also been used for more extensive and specific tests, which are carried out by specially recruited laboratory technicians. In the meantime, the LCC is no longer just there to ensure a consistently high standard of our labels, but also takes on numerous development tasks.
We constantly put our labels to the test and look for ways to make them even better, more resistant or more flexible. In the same way, however, the LCC also develops custom-fit solutions to perfectly meet customer requirements. Since many test procedures take several weeks (e.g. to research bonding times), several tests are always carried out there in parallel.
Special features of the LCC
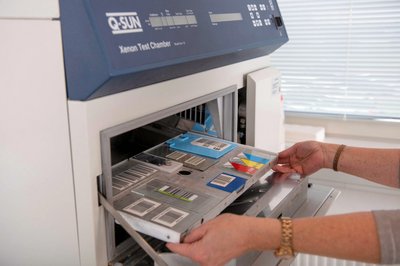
By permanently checking existing labels, we can guarantee the consistent quality of existing products. We also continuously update the technical data sheets for individual products in the course of quality assurance. This means that they are always up to date, which makes it easier for our customers to select the right product for their needs.
Another special feature of the LCC is the development of individual products adapted to specific needs. To do this, we look at a specific industry and produce labels that fully meet that industry’s requirements. This results in labels that are tailored to the requirements of a market segment and facilitate their specific logistics processes.
Of course, we can also go one step further and develop or enhance products in the LCC based on completely individual customer requirements. For example, we can test the adhesive strength of our labels directly on customer products or carry out high-pressure washing tests. Last but not least, we offer our customers the opportunity to design products specifically according to their requirements by selecting new materials and material combinations and validating them in the LCC. The end result is absolutely individual labels based on the customer's conditions and wishes.
Test procedures in the LCC
Standardized test procedures play an important role in quality assurance and product development. We can carry out a wide range of these in the LCC, including:
- High-pressure washing test: simulation of a washing line in the food industry (labelling on food containers)
- WOM test: simulation of weathering for labels based on ISO 4892-2, method A, cycle 2
- ISO 18000-6C Query: Selection of a transponder suitable for the intended use
other tests used in the LCC
- Abrasion test
- Chemical Resistance
- heat test
- IPA test (isopropanol-alcohol test)
- cold test
- Adhesion test according to DIN EN 1939
- Van Laar test geometry
- Leach test
- material strength
- MEK test (methyl ethyl ketone test)
- Tapestry test
- Centrifugal test
- Evaluation according to ISO/IEC 15416:2016 and ISO/IEC 15417:2007
More Info